 |
|
 |
 |
 |
|
Question & Answer No.01 |
 |
プレーン層とTHの接続はなぜサーマル接続しているのでしょうか。また、すべての穴をサーマル接続にする必要性はあるのでしょうか。
 |
 |
プレーン層とTHの接続が塗りつぶし(ベタ接続)だと、部品実装ではんだを溶かす際に熱がTH外周から奪われてしまい、
はんだが溶けづらく、結果的に実装不良を引き起こすといった可能性が生じてしまいます。
そこで、プレーン層とTHを配線で接続(サーマル接続)することで、
プレーン層への熱を伝わりにくくし、はんだを溶けやすく、部品実装の効率を上げることができます。
はんだを溶かす必要性がないTH(ビア)であれば、塗りつぶし(ベタ接続)でも大丈夫です。
THの用途/目的によって使い分けを行ってください。
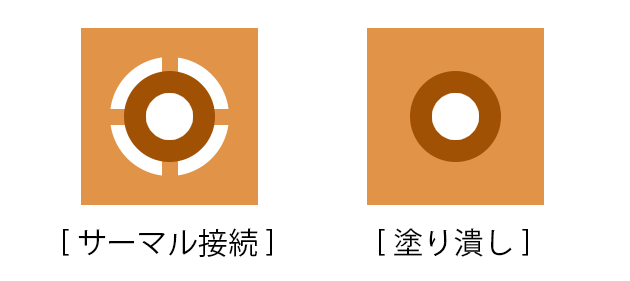
 |
 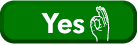
 |
|
|
|
 |
 |
 |
|
Question & Answer No.02 |
 |
板厚0.6mm基板を注文したところ、表面処理中に基板が割れたと工場から連絡がありました。どうして割れてしまったのでしょうか。
 |
 |
はんだレベラーとは、基板をはんだ槽に浸しパッドや端子部にはんだコーティングする方法です。スルーホールにはんだが埋まってしまうため、はんだ槽から基板を引き出す際に熱風を吹き付け、埋まったはんだを吹き飛ばします。
高温で基板が弱くなっている状態で、穴に埋まったはんだを強い熱風で吹き飛ばすため、特に薄い基板では割れやクラックが発生しやすくなります。
このため、板厚0.8mm未満の場合、はんだレベラーは、基板が割れる可能性がございます。
薄い基板を注文される場合は、耐熱プリフラックス処理等の表面処理をご推奨致します。
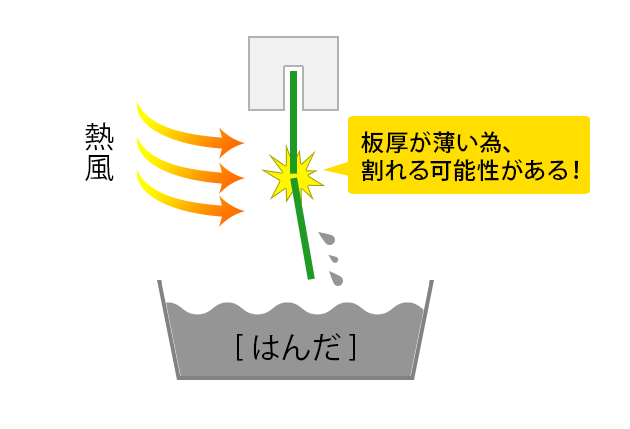
 |
 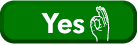
 |
|
|
|
 |
 |
 |
|
Question & Answer No.03 |
 |
パターン設計においてIC下の配線を避けた方がいい理由はなんでしょうか?
 |
 |
ICボディ下に配線をした場合、IC自体からでるノイズの影響を配線が受ける可能性がございます。
その為、ICの下側は極力GND配線にし、配線は部品の外側へ引き出す事をご推奨致します。
また部品の外側へ配線を引き出す事により、部品実装後も基板上で配線の繋がりを確認できるので、パターン修正を行ないやすくなります。
 |
 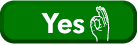
 |
|
|
 |
 |
 |
|
 |
4層基板を設計していますが、GNDと電源は2、3層で配線しております。
GNDと電源は2、3層どちらに配線すればいいのでしょうか。また、2、3層以外にGNDと電源を配線してはいけないのでしょうか。
 |
 |
GNDと電源は2、3層どちらでも結構ですが、GNDの方が電位が安定しているので、高速信号配線が多い配線層に近い方をGNDプレーンにする事をお勧めします。
またGNDと電源は、どの層に入れても製造は可能ですが、表面実装部品からの配線のし易さから配線を表面層(1、4層)に配置するのが一般的です。配線が表面層にあれば、基板上での配線確認や、
テスターやオシロスコープでの信号確認も簡単になります。また、設計変更が発生した場合でも、表面層であれば、パターンのカットやジャンパ配線が簡単に行えます。
EMI対策から、プレーンを1、4層に、信号配線を2、3層に配置する設計もあります。お客様の仕様にあった層構成をご選択ください。
 |
 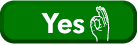
 |
|
|
|
|
|
|
|
 |

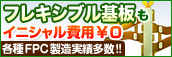
|
 |
|
P板. comの各種サービスに関するご質問はお気軽にお問い合わせください。
Mail: info@p-ban.com Tel: 0120-439-296 Fax: 0120-439-397
http://www.p-ban. com
|
|
|

すべての著作権は株式会社ピーバンドットコムに帰属します。
Copyright © 2014 p-ban. com Corp.Japan. All rights reserved.
|