- プリント基板 P板.com TOP
- 技術ネタ・メルマガ
- テクニカルガイドライン
- 設計者は知らない?! 工場で問題になるデータ
設計者は知らない?! 工場で問題になるデータ
アートワーク設計者は、必ず現状の設計データで製造が可能かチェックをおこないます。ただ、アートワーク設計CADでのチェックは、回路信号をベースとしたパターン接続の確認がメインとなっています。そのため、基板製造時の物理的観点で問題となる箇所のチェックは、設計者の目視でおこなっているのが現状です。
そこで、このたびP板.comでは、製造工程でよく問題になるポイント3点をまとめました。このポイントを知ることで、設計スキルと歩留まりを向上させることができます。今後の基板づくりにぜひ取り入れてみてください。
1ベタ銅はくとパターンの導体間隙に注意
ベタ銅はくとパターンとの導体間隙は、0.3mm程度確保しましょう。
ベタ銅はくとパターンとの間隙距離が近すぎると、銅はくの間にエッチング液が入りにくくなり、その結果、正しいパターン形成ができず回路ショートの可能性が高くなるためです。
一般的にプリント基板は、一枚の銅張積層板の上下からエッチング液を噴霧し、余分な銅はくを削ることでパターンを形成します。バス配線のように銅はく面積が狭い箇所は、パターンの間にエッチング液がうまく入り込み、銅を溶かしていきます。逆に、ベタ銅はくのような銅はく面積が広い箇所には、ベタ銅はくの影響で勢いがついたエッチング液が銅はくの間に入りにくいため、正しいパターン形成ができない可能性が高くなります。
設計データ通りのパターン形成をするためには、ベタパターンと配線やランドのクリアランスは、最小間隙の”2~3倍”以上を確保しましょう。
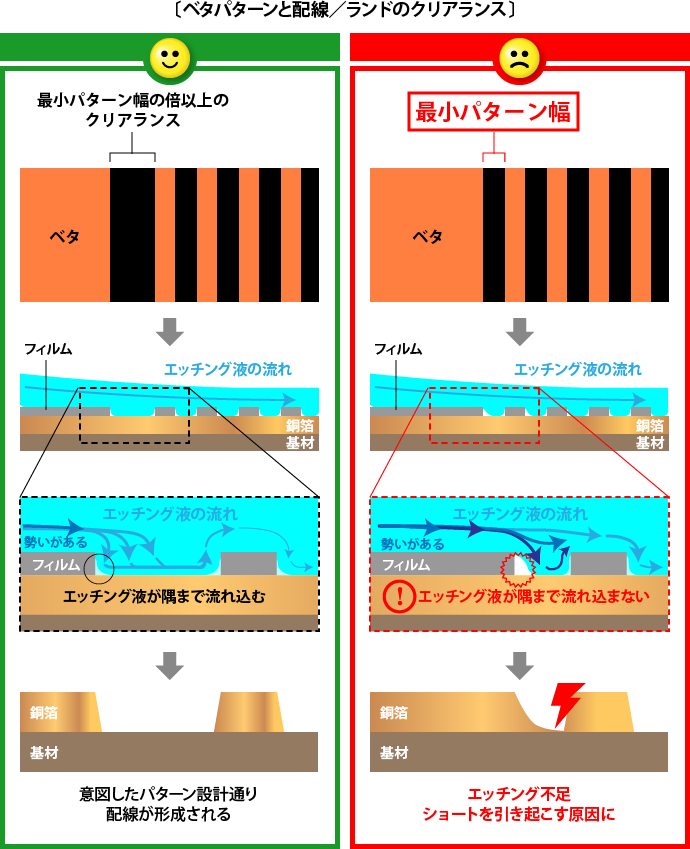
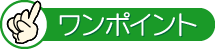
- ベタ銅はくとパターンとの間隙は、最小間隙の2~3倍以上は確保しましょう。
- 最小間隙でガードが必要な場合は、ベタ銅はくではなくパターンを使用しましょう。
2鋭角、微細な形状、微小な間隙に注意
鋭角、微細な形状は避け、微小な間隙は塗り潰してデータを出力しましょう。
パターンデータに鋭角や微細な形状、微小な間隙(以下、「スライバ」という)が存在すると、ショートや断線の原因になるためです。
スライバは、エッチング工程中にドライフィルムが剥離しやすい形状です。剥離したドライフィルムがゴミとなり、工程の薬液に浮遊し他の基板に付着することがあります。その結果、意図しないパターンが形成され、最悪な場合はショートや断線などを起こすことにつながります。
スライバは、アートワーク設計で自動ベタを使用した時に発生しやすいです。自動ベタ使用時は、歩留まりを上げるためにも、スライバが発生していないか確認をし、発生していた場合はスライバを除去するデザインへ修正をしましょう。
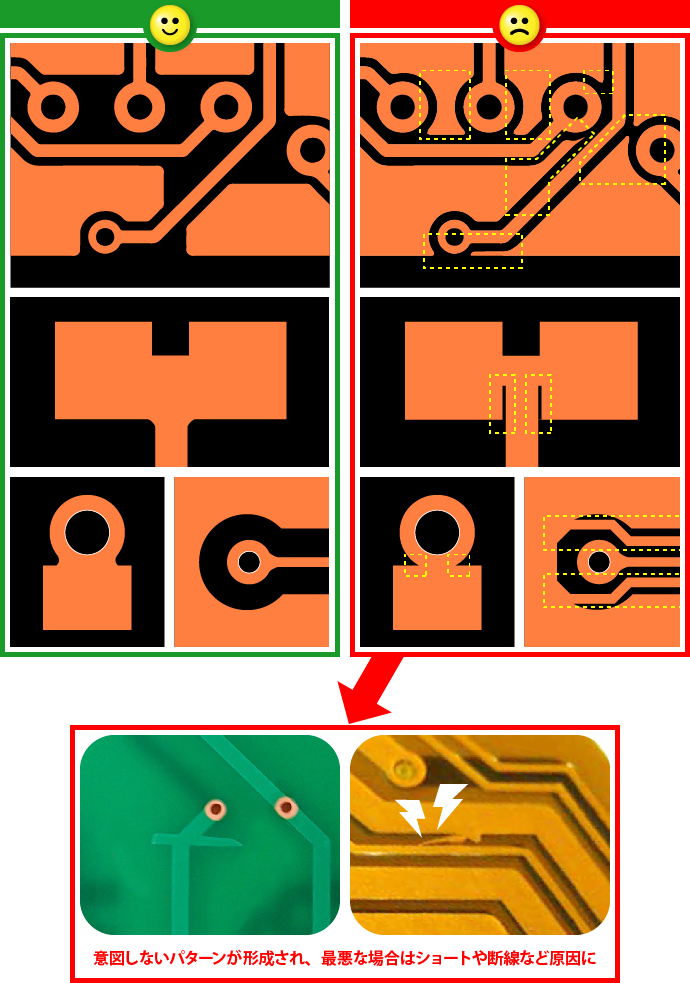
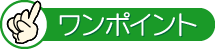
- アートワーク設計では、同ネットの間隙も確認しましょう。
- 自動ベタの線幅を極力太くしましょう。
- 製造前にガーバーデータを印刷し、スライバないかを目視で確認しましょう。
3スリット幅に注意
スリット幅は2.0mmを標準として設計しましょう。
スリットは、外形加工と同じタイミングで加工するため、ルータービットを使用して加工を行います。基板材料が柔らかいFR-1主流の時代には標準スリット幅は”1.0mm”でしたが、FR-1よりも堅いFR-4の使用が標準となった現在では、太いドリルビットを使用する必要性からスリット幅は”2.0mm”が標準となっています。
現在でもφ1.0mmなどの細いルータービットはありますが、細いものはビット折れが発生しやすいため、不良の原因となります。また、折れないよう加工移動速度を遅くしなければならないため、全体の製造時間が増えてコストアップにもつながり、あまり推奨しておりません。
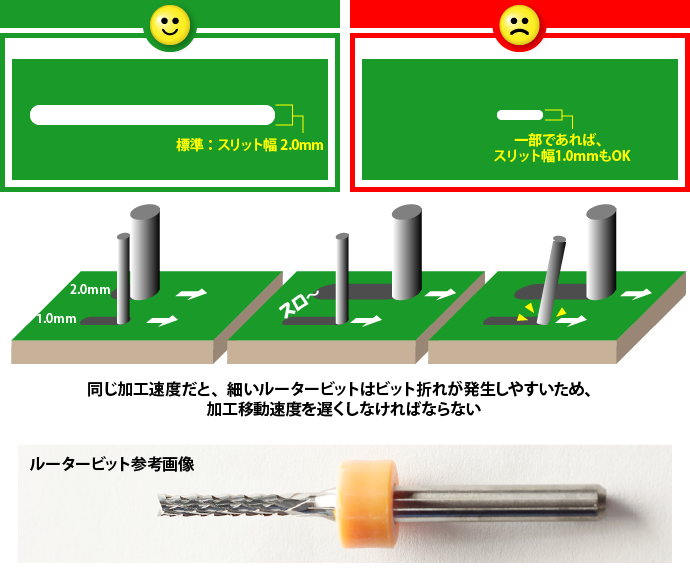
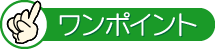
- スリット幅は、”2.0mm”を標準としましょう。
- スリット幅”1.0mm”も使用は可能です。ただし、極力使用は避けましょう。