- プリント基板 P板.com TOP
- 技術ネタ・メルマガ
- テクニカルガイドライン
- 失敗しない製造データのポイント 品質安定編
失敗しない製造データのポイント 品質安定編
試作・リピート製造(量産)に関わらず、安定した品質の基板をつくるには「後工程を考慮したデータ作り」を目指す必要があります。ただ漫然と設計してしまったデータでは、均一な基板仕上がりに影響を及ぼすことがあるためです。
本ページでは、失敗しない製造データのポイント基礎編に続く「品質安定編」として、試作でもリピート製造でも役にたつ設計ポイントをまとめてみました。今後の基板づくりにぜひ取り入れてみてください。
1基板コーナーにはRをつける
基板コーナーには、半径5.0mm程度のRを設けましょう。
基板コーナーにRをつけると、以下のようなメリットがあるためです。
- 基板を取り扱う際の、身体への擦り傷を防ぐ
- 基板製造時や使用時に、他基板やモノの破損を防ぐ
- 実装時の搬送ラインに引っかからず、基板、部品の損失を防ぐ
- 運送時の衝撃、振動による基板の欠けや梱包材の破損を防ぐ
Rは大きい方がよく、R5.0mm程度を推奨します。小さいRでは上記の事象を防げない場合があります。捨て基板、製品基板ともに、コーナーにはRをつけることをご検討ください。
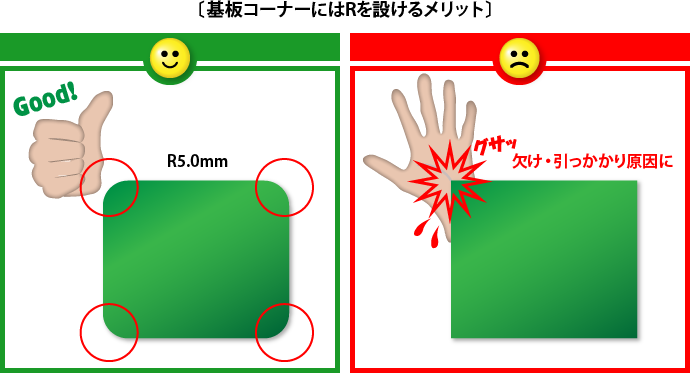
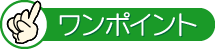
- 捨て基板だけでなく、製品基板にもRを設けましょう。
- R5.0mmが厳しい場合は、可能な限り大きなRを設けましょう。
2捨て基板を追加する
面付けやマウンター実装をしない場合でも、捨て基板の追加を検討しましょう。
外周に捨て基板を設けると、以下のようなメリットがあるためです。
- 基板製造~梱包、出荷工程間で基板製品を傷つかないようにする
- マウンター実装に対応しやすくする
- 製品外に加工ガイド穴、実装認識マーク、基準穴、副基準穴、コーナーRを設置できる
捨て基板は、面付けやマウンター実装時用に使うだけでなく製品を守る効果があるので、基板の上下左右全てに設けることが望ましいです。上下左右への追加が厳しい場合はマウンター実装を考慮して基板の長手方向に設けるとよいでしょう。
基板の面積が増えコストが上がるという点はありますが、品質を安定させる上では非常に効果的な方法です。ぜひ捨て基板の追加をご検討ください。
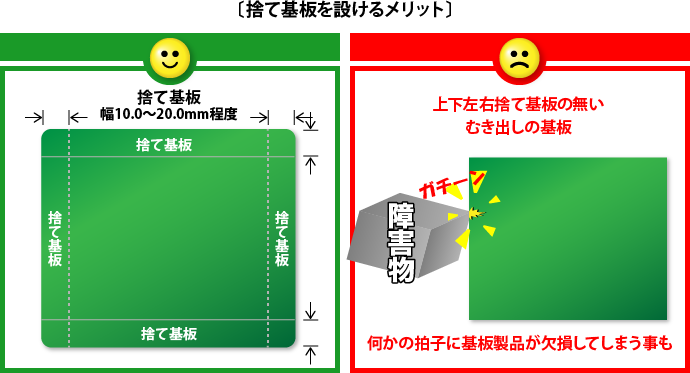
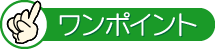
- 捨て基板の幅は通常10.0~20.0mm程度です。
- 反りや伸縮対策のため、捨て基板に分割したベタ銅箔を追加するとよいでしょう。
3加工ガイド穴をあける
安定した外形を作るために加工ガイド穴を設けましょう。
<推奨>
・サイズ:φ2.05mm(NTH)or φ1.55mm (NTH)
・配置位置:基板上に2箇所、逆投入防止用に1箇所、計3箇所
・非対称、非点対称位置に配置
・裏返しても180度回転させても重ならないよう基板対角上に配置
・基板原点座標より5.0mm単位を基本に配置
外形加工に必須の加工ガイド穴を「基板内」へ設けると、次のようなメリットがあるためです。
- 加工ズレを防ぐ
- 一つの工程で外形加工が可能になる
- 外形カット後の基板を支持し落ちないようする
基板内に加工ガイド穴がなくても製造は可能ですが、その場合は基板の全周をルーター加工で全部削り落とさずに外形の一部を残し、手動でカットし基板側面を手加工で平らにして製造します。全部削り落してしまうと、接続部分を切り離す瞬間に応力がかかり基板が飛んでしまうおそれがあります。
正しい外形を作成するためには、ぜひ加工ガイド穴の設置をご検討ください。
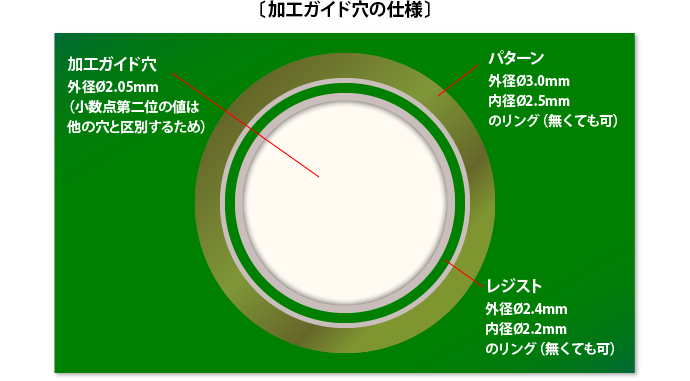
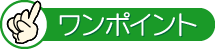
- 基板サイズが330mmを超える場合は、対角の中間点にも追加しましょう。
- 加工ガイド穴周辺に次のようなガード用パターンを設けると、一目で認識できます。
パターンサイズ:外形φ3.0mm、内径φ2.5mmのリング
レジストサイズ:外形φ2.4mm、内径φ2.2mmのリング - 基板密度によっては、基板原点座標より1.0mm単位での配置も可能です。
4基準穴/副基準穴をあける
実装工程で使用する基準穴/副基準穴を設けましょう。
<推奨>
・基準穴:φ4.0mm(NTH)
・副基準穴:φ4.0x5.0mm(LNTH)
・実装流し方向に対し水平に配置
基準穴/副基準穴を設けると、次のようなメリットがあるためです。
- マウンター実装機に基板を取り付ける基準穴となる
- 基板を固定し実装ズレを防止する
- 自動挿入機を使用しリード部品を差し込む際の「位置決めの基準穴」となる
副基準穴は、基板の寸法収縮を考慮して丸穴ではなく長円としています。「基準穴/副基準穴」が必要ないSMD部品のマウンター実装機もありますが、位置決め用の基準ピンやマウンター内の搬送用のピンを使うマウンター機器が多数あるため、設けておくことを推奨します。
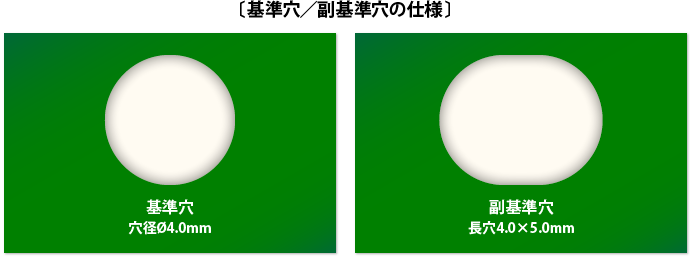
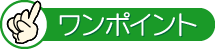
- 複数穴を追加すると、基板の流し方向がどの方向であっても対応できます。
- 基準穴径はφ4.0mm、φ3.5mm、φ3.0mm とし、追加時は大きいサイズを優先しましょう。
5実装認識マークをつける
挿入機や装着機と基板の位置合わせをするための、実装認識マークを設けましょう。
<推奨>
・パターンサイズ:φ1.0mm
・レジスト開口サイズ:φ3.0mm
・ガードパターン:外径φ3.9mm、内径φ3.3mm のリング
・配置位置:基板上に2箇所、逆投入防止用に1箇所、計3箇所以上
・非対称、非点対称位置に配置
実装認識マークを配置すると、以下のようなメリットがあるためです。
- マウンター実装で部品を自動挿入、自動装着する際の位置合わせとなる
実装認識マークがないとマウンター実装ができない場合もあるので、設けるようにしましょう。また、0.5mmピッチ未満の狭ピッチ部品や、BGAなどのパッケージの下にリードがある部品は、マウンター実装の精度を高めるために個別に設けることを推奨します。
配置位置は、表面、裏面の誤実装を防ぐためにも非対称、非点対称とし、裏返しても180度回転させても重ならないようにします。こうすることで、仮にマウンターへ逆に投入されたとしても、部品搭載ミスを防ぎます。
なお、パターン形成時のエッチング(銅箔の不要箇所を化学薬品の腐食作用で溶解していく工程)により実装認識マークが消えないようにするため、保護目的で周りにベタパターンを配置するとよいでしょう。
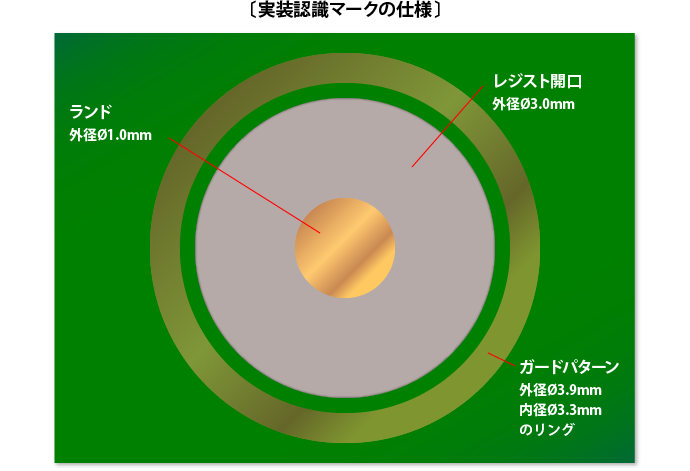
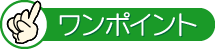
- お客様指定の認識マークでも対応可能です。
- 面付けの場合は、各単面基板にも認識マークを設けると精度が上がります。
6 品番/機種名を表記する
基板を特定する品番、機種名などを表記しましょう。
基板を特定する品番、機種名などを表記すると、以下のメリットがあるためです。
- 一目でどの基板か認識できるようになる
- 類似基板との取り間違いを減らす
何も表示がない場合は、基板の絵柄で判断することになってしまいます。品番、機種名などを表記することで、取り間違いを減らします。また、改版時に「通し番号」などの記載があると細かい変更をした際にも目視確認でき、管理しやすくなります。
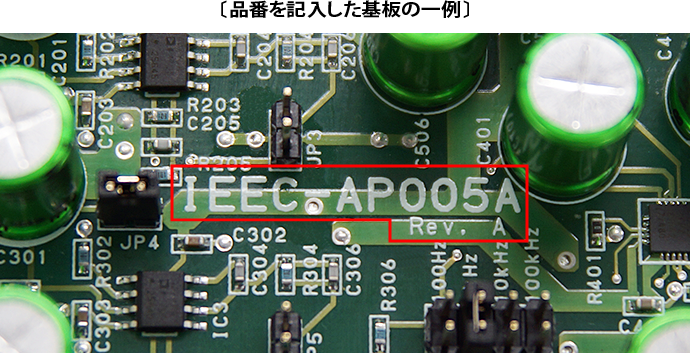
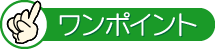
- 第三者にも分かるように、大きく目立つ場所に表記しましょう。捨て基板などに表記すると、部品番号などの他の文字と区別できます。