- プリント基板 P板.com TOP
- 技術ネタ・メルマガ
- テクニカルガイドライン
- 失敗しない製造データのポイント 基礎編
失敗しない製造データのポイント 基礎編
プリント基板はガーバーデータをもとに製造します。P板.comおよびプリント基板製造工場では、必ずデータのチェックを行ってから製造へと取り掛かります。データチェックで気になる箇所が発見された場合は、お客様(データ設計者)に確認し修正をお願いしています。
いつもたくさんのデータをご確認させて頂いているP板.comが、失敗しない製造データのチェックポイントを8つにまとめました。ぜひ、今後の基板づくりにお役立てください。
1アニュラリングの確保
アニュラリングは、穴径の大きさで変化します。以下の基準を確保してください。
≪ 穴径がφ1.0mmより大きい場合 ≫・ランド径 = 穴径 x 1.5 [mm]≪ 穴径がφ0.6mm以上φ1.0mm以下の場合 ≫・ランド径 = 穴径 + 0.5 [mm]≪ 穴径がφ0.6mm未満の場合(部品を挿入しないビア穴に限る) ≫ランド径 = 穴径 + 0.3 [mm]
※ φ0.3/0.5mm、φ0.25/0.5mm、φ0.2/0.45mm、φ0.15/0.4mm、φ0.15/0.35mm は、対応可能です。それ以下のビアについては、個別見積で対応いたします。
プリント基板の一般的な製造は、すべての穴に銅めっきを施したあとに、不要な銅をエッチング液で溶かしパターン形成をしていきます。スルーホール(以下、THと言います)の穴内にエッチング液が入ると、銅めっきが除去されて電気導通しなくなってしまうため、テントの役割をするドライフィルムを張っています。このテントの土台となる箇所がアニュラリングです。アニュラリングが小さいとテントが破れやすくなるので、基準値以上を確保する必要があります。
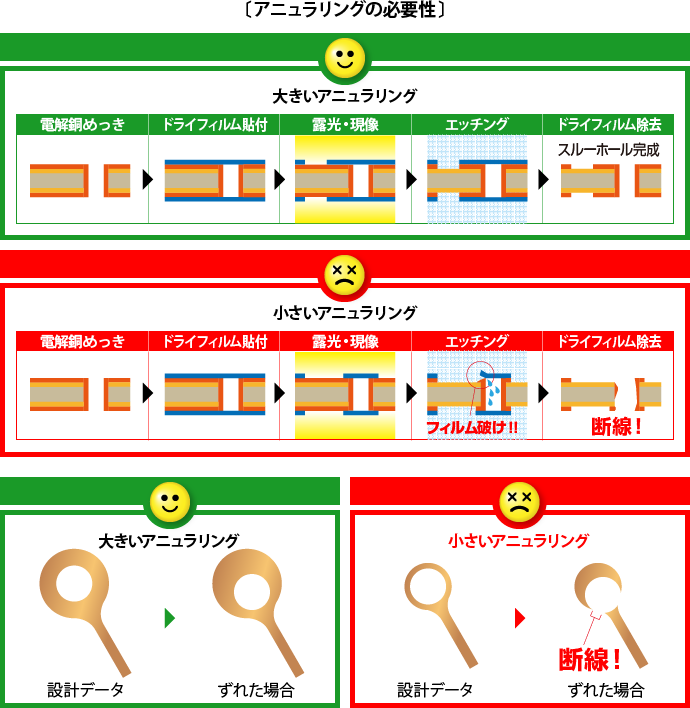
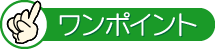
- アニュラリングに余裕をもった大きさがあると、穴やパターン位置がずれた際の断線などを防ぐことにもつながります。
2線幅のチェック
線幅0.01mmのような細い線幅による塗りつぶしはやめましょう。
ベタの塗りつぶし線幅を0.01mmのように細く設定すると、CADの特性によって指定した線幅未満のデータが作成されてしまうためです。
また、塗りつぶし線幅が細いほどデータ容量が重くなり、ガーバーデータの出力や送信、各工程での確認作業でも時間が掛かってしまい、お急ぎの案件では遅れにもつながります。ベタの塗りつぶし線幅は、最小パターン幅以上の値を設定しましょう。
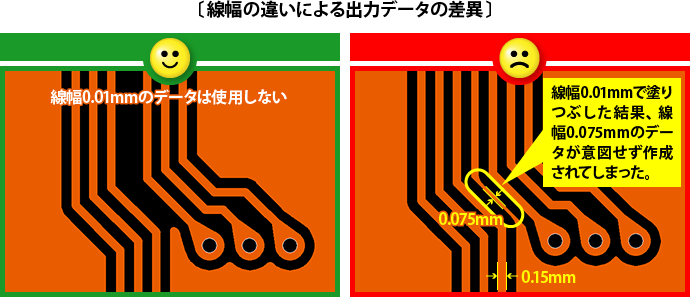
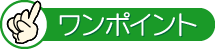
- 最小パターン幅未満の値を使用していないか、ガーバーデータ出力時にも確認しましょう。
3外形から銅はくまでの距離
外形から銅はくまでの距離は0.3mm以上で作成しましょう。
外形と銅はくの距離が近すぎると、外形をルーター加工した時に基板の側面から銅はくが露出してしまうことがあるためです。銅箔の露出は、別の層や外部の導電体とのショートを引き起こす危険があります。
なお【0.3mm】は、銅はくや外形の製造公差から計算される最低限必要となる数値です。安定して良い品質の基板を目指すには【1.0mm】以上の間隔を推奨します。
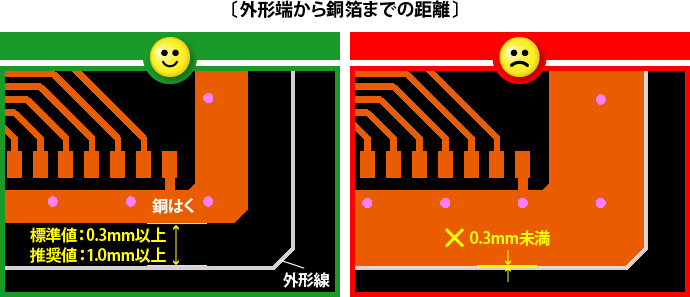
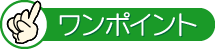
- 外形端と銅はくが接しているデータでも製造することはできます。その場合は上記をご理解いただいた上で、ご注文時の指示欄に「外形線とパターンの近い箇所はデータ通りで問題ない、基板端面からの銅箔露出を了承する」とのコメントをお願いします。
4同ネットも最小配線間隙を確保
同ネットの銅はくも最小配線間隙を確保しているかチェックしましょう。
<特にチェックする箇所>
・面データの塗りつぶし箇所
・部品パッドからの引き出し
・ミアンダ配線
ガーバーデータ上ではネットの概念がないため、設計データが同ネットでも「配線間隙が不足している箇所に問題があるか」を設計者に確認する必要があるためです。また同ネットとわかっていても、工場側で製造可能なようにデータを補正する場合もあります。補正せずに製造した場合、パターン形成の工程でドライフィルムがはがれて屑を発生させる可能性があります。この屑が原因でパターンショートやオープンを引き起こすため、同ネットであっても配線間隙を確保する必要があります。
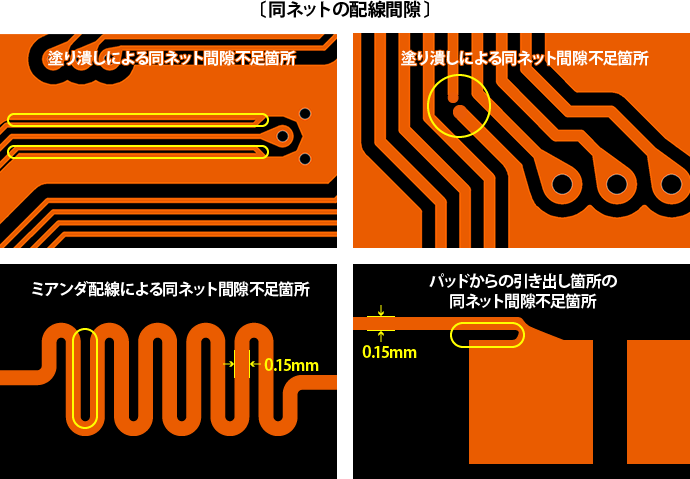
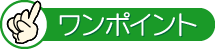
- 面データの塗りつぶし箇所、部品パッドからの引き出し、ミアンダ配線などに多く見られます。ガーバー出力前後に確認してみましょう。
5長穴データの指定方法
長穴は「ドリルデータの連打」+「外形線に長穴形状」で作成しましょう。
<長穴データの指定方法>方法1:ドリルデータの連打で長穴形状を作成(0.1mmピッチで連打)
方法2:外形線に長穴形状を作成(長穴の穴径と長さ指示が必須)
長穴のご指定は、方法1「ドリルデータの連打」のみ、あるいは方法1、2を組み合わせた「ドリルデータの連打+外形線に長穴形状」を推奨します。
製造工場では「ドリル加工」によって長穴を製造しますので、方法2「外形線に長穴形状」の場合には、製造工場の作業者によってドリルデータを追加・編集する必要があります。その際に、設計者の考えが正しく伝わらずに異なる長穴を作ってしまう可能性もありますので、長穴は「ドリルデータの連打」+「外形線に長穴形状」で作成しましょう。
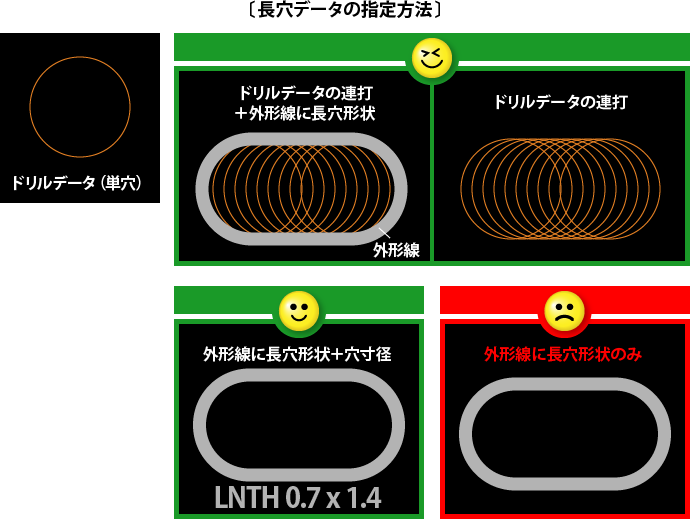
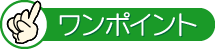
- CADの長穴機能を使った場合は、ドリルデータが正しく作成されているか必ず確認しましょう。
6レジストの線幅
レジストの線幅は、以下の基準を確保してください。
≪レジスト色:緑/赤/青/黄/紫 の場合≫最小線幅:0.1mm
≪レジスト色:白/黒/黒(つや消し) の場合≫最小線幅:0.2mm
部品(特に狭ピッチ部品)のパッド間には、部品実装時のはんだブリッジによる回路ショートを防ぐためにレジストを塗布することを推奨します。なお、レジストの色味ごとに顔料の成分や露光特性の違うため、最小線幅が異なります。色の選定にもご注意ください。
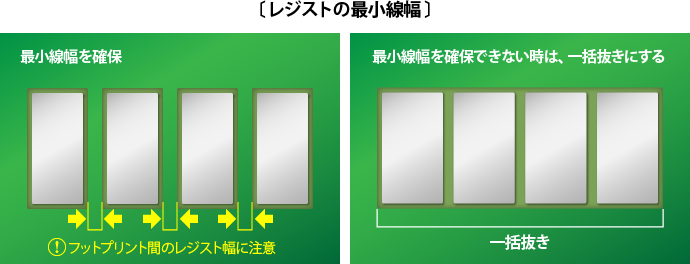
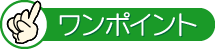
- 狭ピッチ部品は、レジストの最小線幅を確保しているか再確認しましょう。
- 最小線幅を確保できない部品は、レジストを一括抜きにしましょう。
7部品パッド部の確認
ガーバーデータの出力前後に、部品のパッド部にレジスト開口が正しいかを再確認しましょう。
CADで正しくレジスト開口が設計されていても、ガーバー出力時に層選択を間違えたなどにより、正しく開口がされないことがあります。部品パッド部にレジスト液が塗布された基板は部品が実装できないので使い物になりません。この点は要注意です。
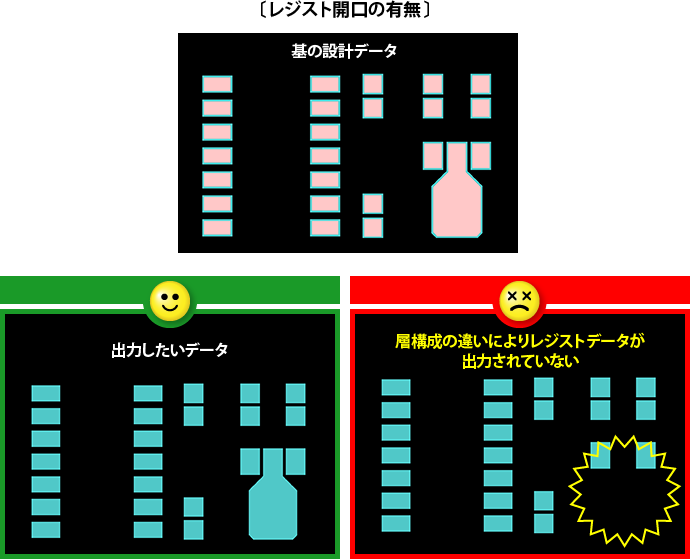
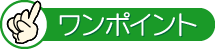
- 自ら製作した部品だけでなく既存の部品ライブラリも含めて、アートワーク設計の前に「現在の設計環境で全層が出力されているか」を確認することをおすすめします。
8シルクの線幅と文字高さ
シルクの線幅と文字高さは、以下の基準を確保してください。
<推奨値>線幅:0.150 mm以上、文字高さ:1.50 mm以上
<最小値>線幅:0.127 mm以上、文字高さ:1.00 mm以上
上記の最小値を下回ると、うまく印刷できず文字が判読できなくなる可能性があるからです。シルクは、一般的にスクリーン印刷と呼ばれる化学繊維を網目状にした版材からインクを押し出す工法を使用するため、設定値が小さいと十分なインクが網目を通らず、にじみやかすれが出やすくなります。
さらに、プリント基板は銅はくの凹凸があるため、設定値が小さい場合は真っ平らな紙に比べてより印刷性が下がります。これらの理由より、上記の値以上の大きさを確保することを推奨します。
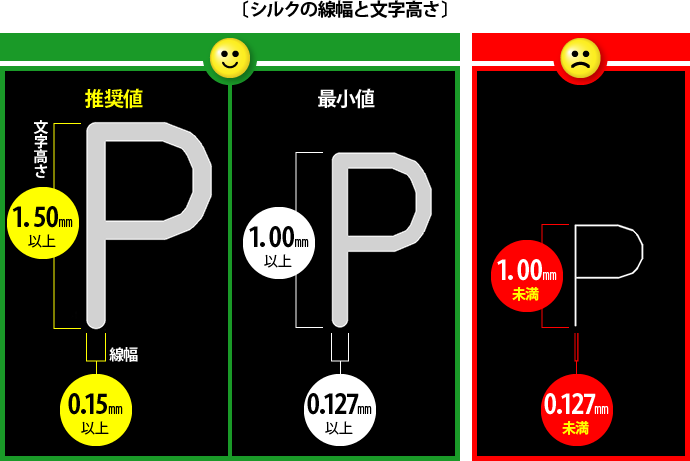
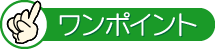
- 文字高さの寸法は実測値です。CADのテキスト入力値ではないのでご注意ください。
- 等倍寸で紙に印刷して、認識できる文字かどうか確認しましょう。できるだけ大きくすることを推奨します。
- シルクを入力するスペースが少ない場合は、プリント基板上で確認したい文字のみを入力しましょう。